Study evaluates performance of different single-well geothermal borehole designs
A study from the University of Glasgow compares the thermal and hydraulic performance of different single-well borehole heat exchanger systems.
A recently published paper by Christopher S. Brown, Isa Kolo, David Banks, and Gioia Falcone from the James Watt School of Engineering at the University of Glasgow compares the thermal and hydraulic performance of the different types of single-well, medium-depth borehole heat exchanger designs.
The full paper, “Comparison of the thermal and hydraulic performance of single U-tube, double U-tube, and coaxial medium-to-deep borehole heat exchangers,” has been published in the Geothermics journal (https://doi.org/10.1016/j.geothermics.2023.102888)
Design comparison
The three designs being compared in this study are all single-well, closed-loop systems. These designs are very commonly implemented in different parts of Europe and the US. The study states that the typical depth of closed-loop borehole heat exchangers (BHE) in many European countries has been steadily increasing. For the purpose of this study, the middle-deep range is considered to be 500 meters to 1000 meters depth.
In a coaxial DBHEs, fluid is warmed by the natural geothermal gradient as it flows downward through the annual space. The heat is then extracted by pumping the fluid back to the surface via the central pipe, typically at a faster velocity to minimize heat loss.
U-tubes and double U-tubes circulate a heat transfer fluid down and up the hole through fully enclosed pipes, typically made from high density or cross-linked polyethylene. U-tubes can either be suspended within the column of natural groundwater, or sealed in place by a grout with low permeability and high thermal conductivity. The standard outer diameter of U-tubes can vary for each application.
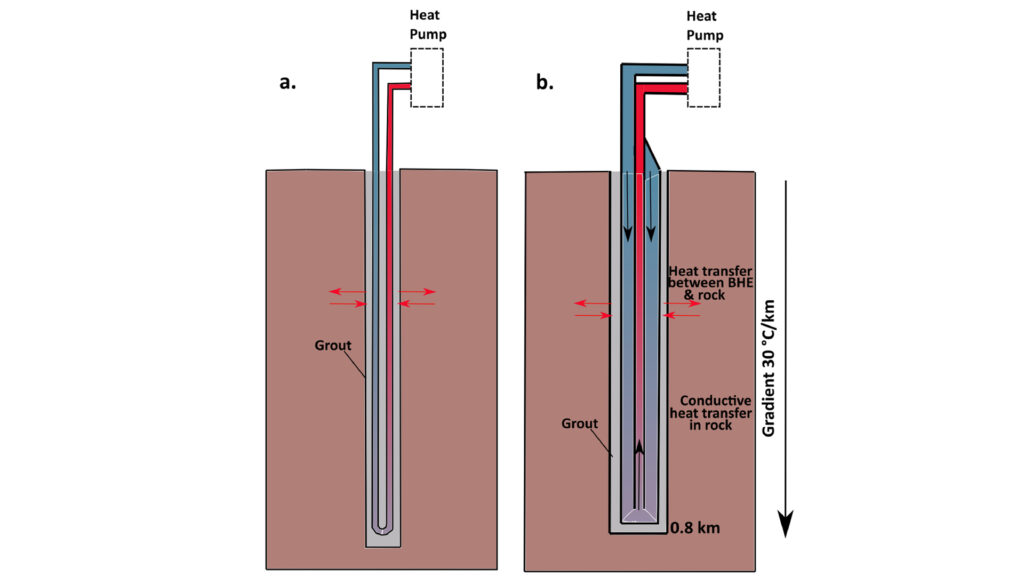
Method and comparison to thermal response tests
Simulations were done using the borehole heat exchanger heat transport module of the open-source OpenGeoSys software. The models consider heat transfer in the rock formation, the grout region, and the inlet and outlet pipes.
Validation of the models was done by comparing the output values to those obtained using actual thermal response tests. The modelled data for U-tube systems have an error of only 0.4% compared to real-world values, while that for coaxial systems had a similar error of ~0.6%
Model response to design parameters
The individual models were then evaluated based on different system design parameters to evaluate heat extraction, pressure drop, and parasitic losses.
- Heat extraction
The coaxial system showed better heat extraction rates, likely due to increased area of contract between the annual space and the surrounding solid rock/grout. In terms of thermal efficiency, the coaxial system was only marginally better than the double U-tube because of other considerations like cost, engineering practicality, and potential pressure losses.
The pressure drop in the system is much lower in coaxial, at 85 kPa, compared to the single U-tube and double U-tube configurations, at 1.46 MPa and 423 kPa, respectively. This then translates to a lower output needed for the circulation pump to run the system for the coaxial configuration, given similar flowrates.
- Depth
Increasing the depth of the borehole increases the outlet temperature and thermal power for all borehole configurations. There is also a linear increase in pressure drop with depth, thus resulting in an increasing pumping power.
- Flow rate
Flow rate had a significant effect on both thermal power and pressure drop. Greater flow rates (> 3 L/s) lead to an increase in heat extraction rates for all configurations, with coaxial providing the highest achievable thermal power. Increasing flow rates correlate to a disproportionate increase in pressure drop for all MDBHE configuration type, indicating that pressure loss is proportional to the square of the flow rate.
Interestingly, the greatest thermal power recorded was for the U-tube configuration model at the lowest flow rate (1 L/s). This was due to greater fluid velocities in the narrow pipe, resulting to greater heat extraction.
- Rock thermal conductivity
Both outlet temperature and thermal power have positive near-linear correlations with rock thermal conductivity, with the highest rate of increase observed in coaxial systems.
Conclusions
The study concludes that coaxial borehole heat exchange perform best in terms of optimizing geothermal heat extraction and minimizing hydraulic pressure losses in mid-to-deep BHEs. The recommendation is then to adopt such design when constructing boreholes at depths greater than 500 meters.
Single U-tubes are viable in scenarios with flow rates of 1 L/s. They, however, provide low thermal output at depth and may have increased parasitic pumping losses at depths beyond 500 meters.
Source: Brown et al., 2024